
Capping, Lamination And Chipping I Tablet Manufacturing Defects I Dr. Muhammad Saquib Qureshi
Capping. Capping is a term used to describe the partial or complete separation of the top or bottom crowns of a tablet from the main body of the tablet [1]. In another word, capping is a laminar splitting along the edge of the crown or band of a compressed tablet [2]. Generally, capping is a common tablet defect during tablet manufacturing.

Capping (2) I Holland
A tablet with high concavity can also be difficult to remove from the lower punch, leading to capping or sticking if insufficient lubrication is present. Logos/Lettering and Embossing Brand identity and the requirement to have logos on tablets can lead to difficulty in adapting the design of a tablet so that the embossing on the tool creates a.
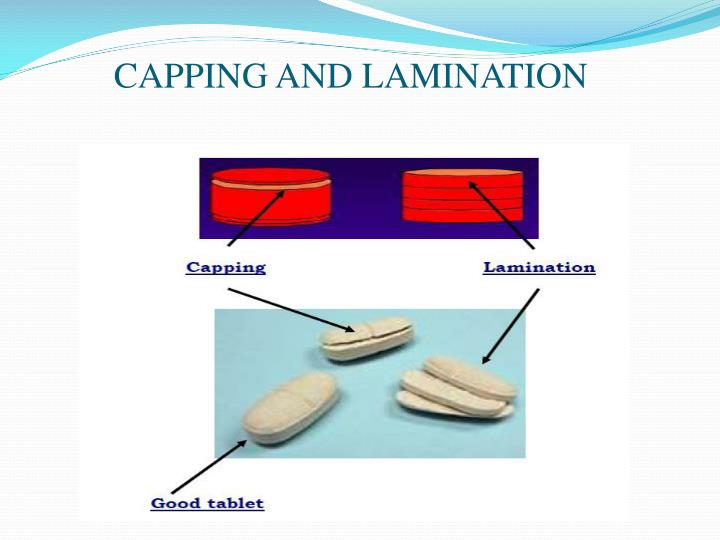
PPT Seminar on DEFECTS IN TABLETS PowerPoint Presentation ID2197543
punches and entire tablet press). โCapping' is the term used, when the upper or lower segment of the tablet separates horizontally, either partially or completely from the main body of a tablet and comes subsequent handling. Reason: Capping is usually due to the air-entrapment in a compact during compression, and subsequent expansion of

The Issue Of Tablet Capping And Its Resolution Senieer What You Trust
Cause: It happens when the penetration controls for the tablet are not set according to the ideal conditions.The ideal range of the control is from 1.5 mm to 2 mm. The main cause of this problem is the entrapped air. When the air is punched too deep in the die, it will not have sufficient room to escape from the tablet, which will later form fractures in the tablet.
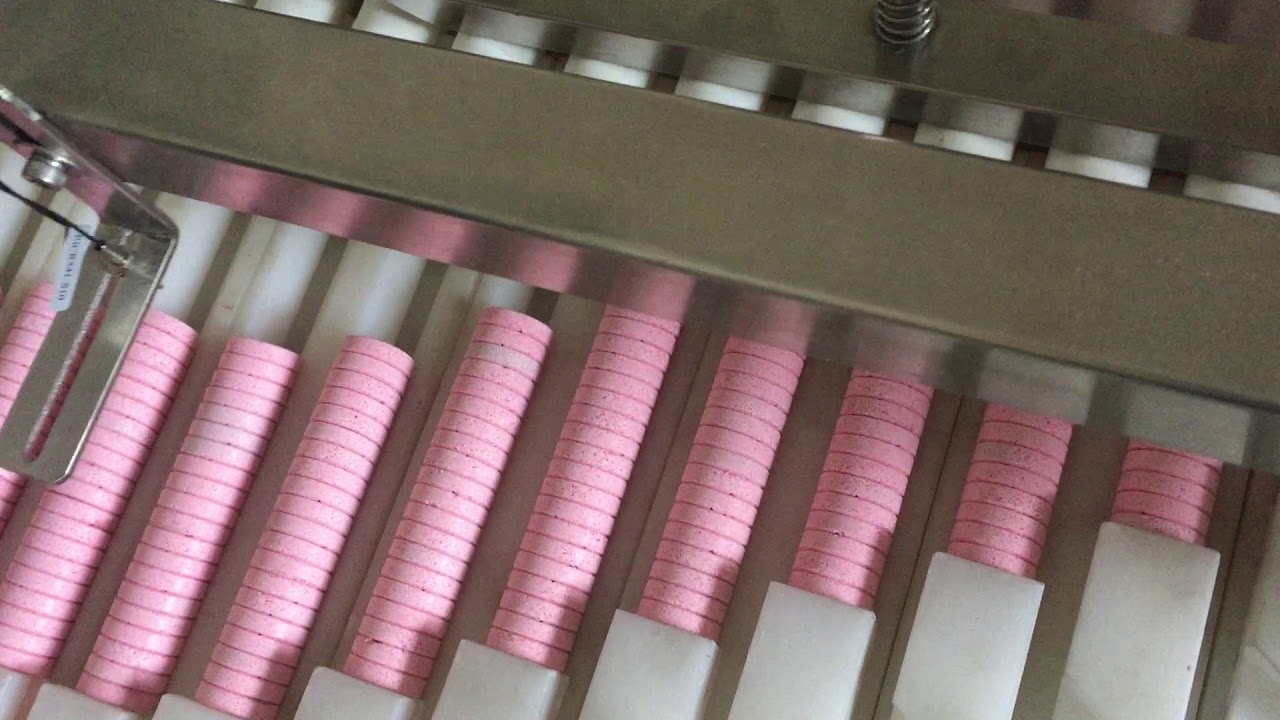
GR80 Tablet Tube Counting Filling Capping Machine YouTube
Causes of Capping. - Entrapped Air: Air can become trapped within the tablet during the compression phase, resulting in capping. -Over compression: too high forces causing too high elastic deformation. -lack of bonding capacity in the power combined with too low bulk density. - Too high tableting speeds leading to short rearrangement times.

Figure 7 Tablet filling, counting and capping SaintyTec
Chipping. Definition: Chipping occurs when the film becomes dented and chipped and this is most notably visible on the edges of the tablet.. Causes: Deformity in the tablet cam occur when there is a decrease in the rotation speed in the machinery during the coating process.Another cause would be a poor polymer or coating solution - e.g., an incorrect amount of plasticizer is used in the.

Belajar Obat Kursus Terjangkau untuk Apoteker dan Pelajar
Capping is a term used to describe the detachment of a cross-sectional fragment from the tablet face, which usually occurs just after ejection of the tablet from the die. The damage to tablets by capping will invariably lead to production batch rejection. For a registered product, changing the formulation is not the preferred option to resolve.

Tablet Capping R.Deckert GmbH & Co. KG
Peristiwa ini menyebabkan capping pada permukaan tablet. Ketika punch atas menekan granul teralu dalam di dalam die, udara tidak mempunyai ruang yang cukup untuk keluar sehingga menyebabkan retak pada tablet. Solusi: Lakukan perubahan ketinggian/kedalaman dari mesin misalnya penetrasi pada 3 mm atau kurang. Dapat digunakan die dengan lubang.
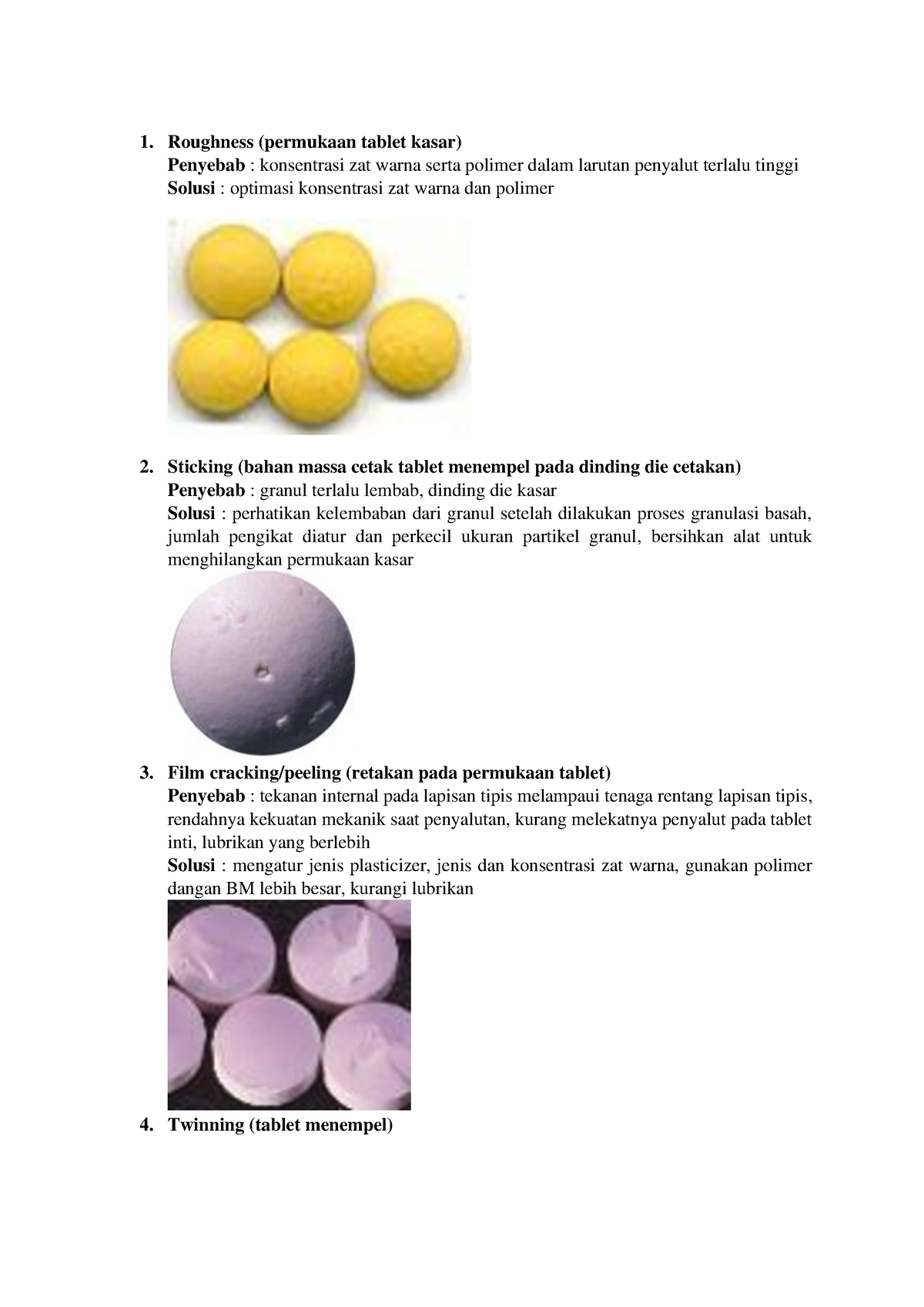
Kerusakan Tablet Roughness (permukaan tablet kasar) Penyebab konsentrasi zat warna serta
Causes of capping and lamination. Presence of air pockets in the granules that is, inadequate removal of air from the granules in the die cavity before and during compression. Presence of too many fines or small and tiny particles in the granules. Undue elastic compression of the tablet due to the use of too high a pressure at the compaction stage.
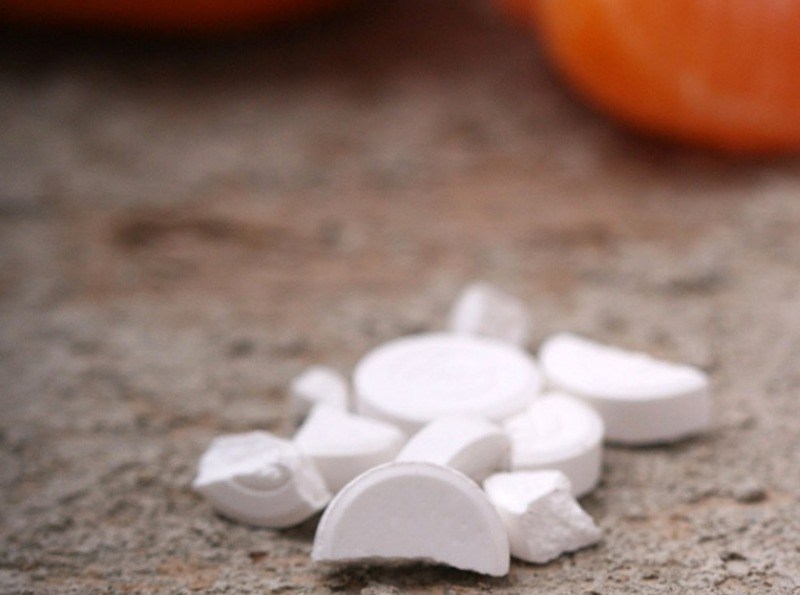
Articles
Solution. Slow down the compression machine speed. By reducing the speed of compression machine, dwell time is increased so it provides more time to compress the tablets in die cavities and after compression proper time is given for relaxation and capping is prevented. Increased dwell time by reducing the machine speed also allows air to escape.

How to.. Capping of tablet presses Fette Compacting YouTube
Capping potential can sometimes be reduced by adjusting the tablet press parameters. One example is by adding pre-compression force. Pre-compression, or de-aeration, is a compression stage before the main compression event where the final compact is made. A low amount of pre-compression force will allow the removal of air between the particles.
Capping Tablet (Pharmacy) Materials
Predicting tablet defects, such as capping, that might occur during manufacturing, is a challenge in the pharmaceutical industry. In the literature, different parameters were presented to predict capping but no general consensus seems to have been reached yet. In this article, we chose to study a wide range of products (18 formulations, 8 of.
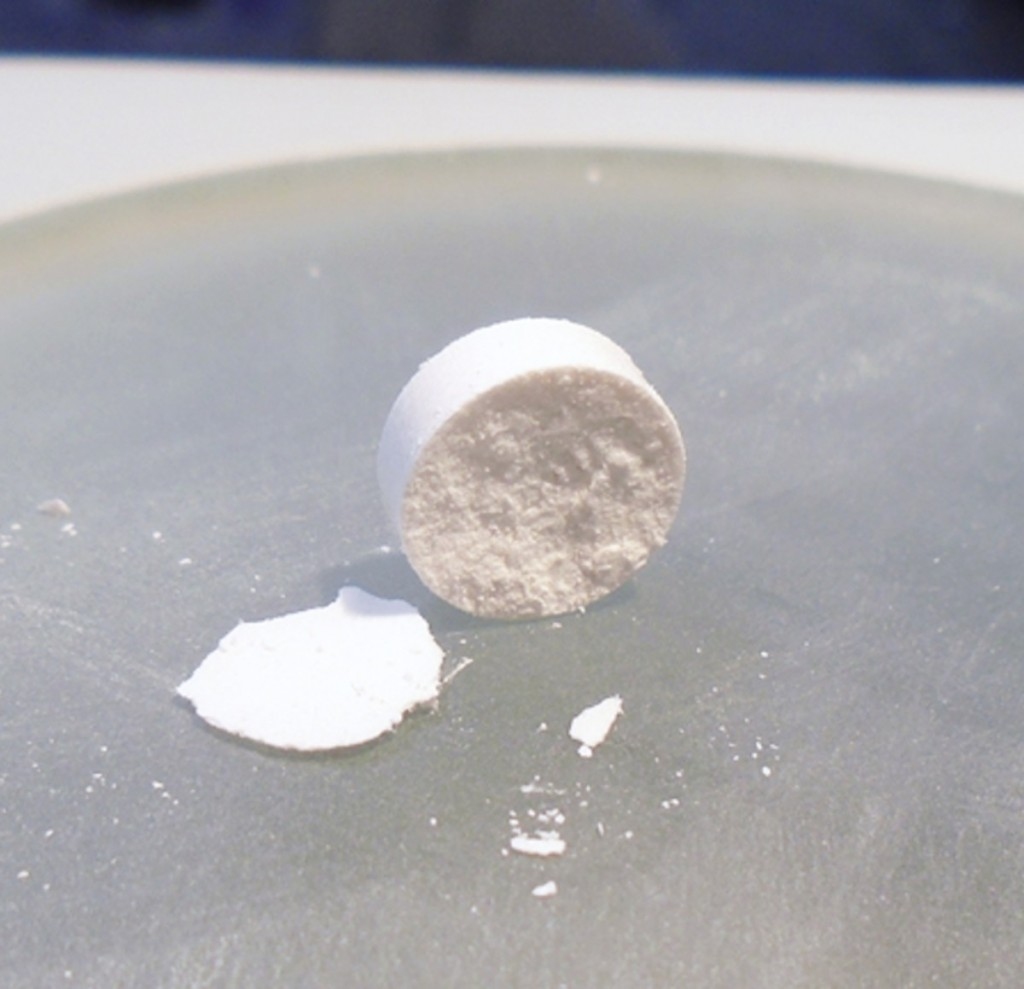
Tablet Capping and Lamination Lamination of Tablets
Tablet capping is the most common defect. It is when the shaped dome of the tablet fractures away from the body of the tablet. When compressing a tablet, the air is pushed out from between the granules, which allows them to be locked together. If the particles are too dry, over-lubricated or highly elastic, they do not bond together sufficiently.
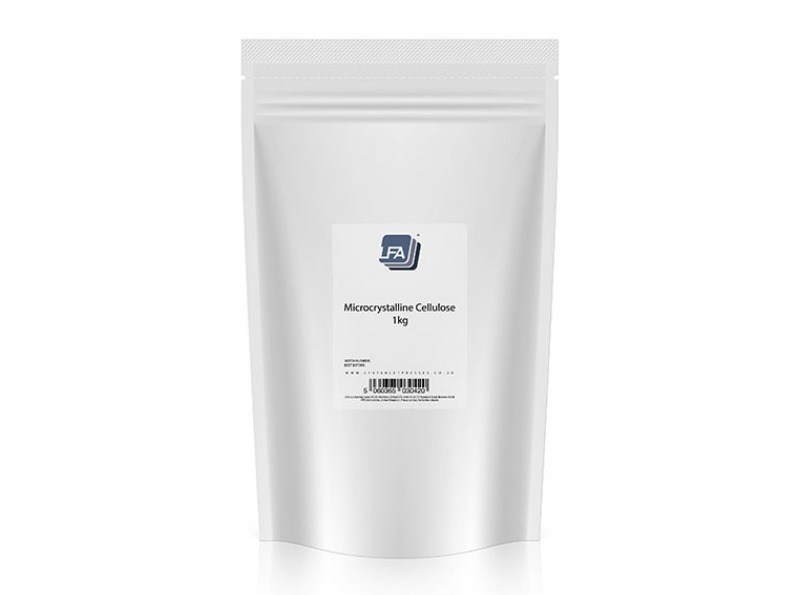
Tablet Capping What is it? How to Avoid Tablets Capping
Capping is an important industrial problem that can arise during the manufacturing of pharmaceutical tablets. It corresponds, for biconvex tablets, to the detachment of one of the cups of the tablet during the ejection from the press or after relaxation. Solutions to this problem remain mainly empirical. Among them, precompression is widely used.One of the most popular explanation of the role.
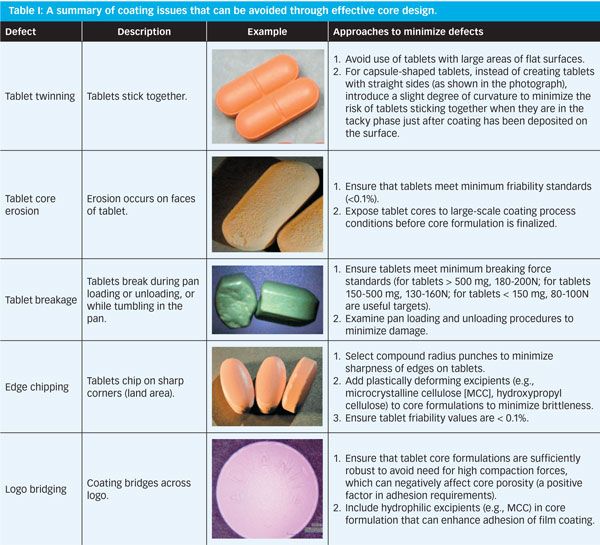
How To Prevent Tablet Coating Problems
Turret speed to reduce tablet capping. Decreasing the tablet press' turret speed may also reduce capping. An acceptable tablet strength might be achieved on a small R&D press, but when moved to production scale, the press may use a higher compression rate or a lower dwell time. If the formulation is strain-rate sensitive, compression speed.
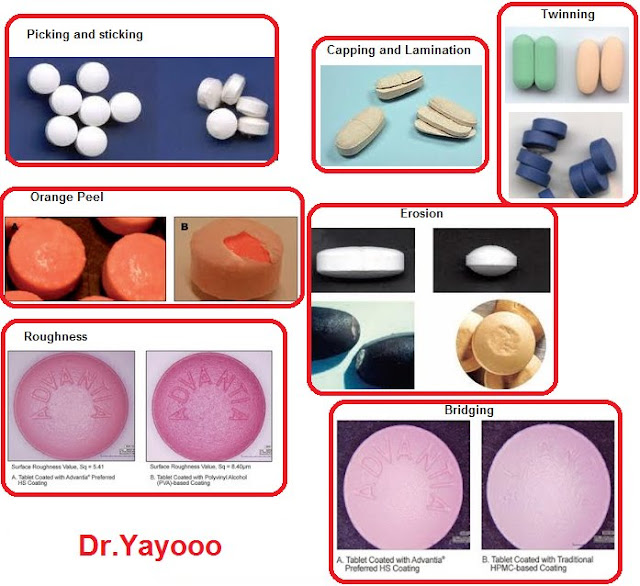
Food, Health and Medicine Coating Tablet Defects The Cause and The Remedies
Predicting tablet capping in terms of process variables (e.g. compaction pressure and speed) and formulation properties is essential in pharmaceutical industry. In current work, a non-destructive contact ultrasonic approach for detecting capping risk in the pharmaceutical compacts prepared under various compression forces and speeds is presented.